Safety in the workplace is a fundamental value of our sustainability culture, as it is the protection of our employees' health.
Safety begins with workers and returns to them as the final objective of the actions we implement for the overall risk mitigation and management. The phases of the process are planned and implemented through the involvement and participation of the workers themselves. Awareness, as a personal attitude, is one of the key factors in accident prevention. Health and Safety is a common value.
The Golden Rules of our Group
We have defined rules and guidelines valid for everyone to standardize behavior, share health and safety best practices and create a Group culture based on common principles.
Our Golden Rules are the operational guiding principles on health and safety at work, issued by Cementir Group at the beginning of 2021 with the aim of preventing accidents and thus protecting employees at work.
The Golden Rules are a prerequisite for developing a proactive and responsible safety culture, where the principle "Each one protects everyone" applies.
Lehigh White Cement is part of this culture where everybody has a role and bears a responsibility to prevent incidents.
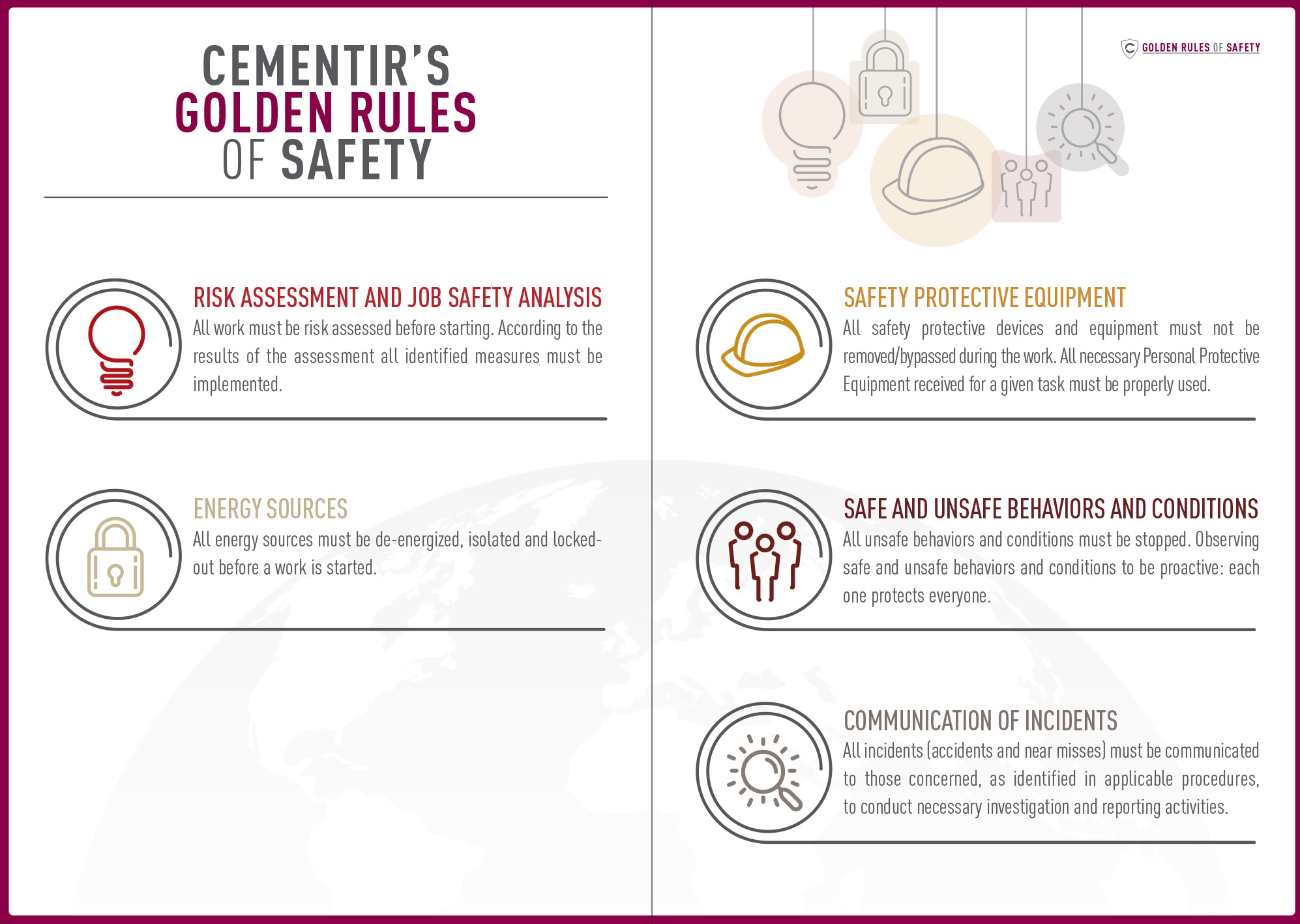
Golden rules
Accident prevention
We are constantly working to prevent injuries. Our commitment is based on the following key requirements.
- Set clear goal and targets and specific action plans with a systemic approach. H&S is an integral part of our strategy.
- Establish clear accountabilities and responsibilities. Respect procedures and rules by workers to guarantee health and safety of all. H&S is a line responsibility. Everybody has a role and responsibility to prevent incidents.
- Identify and assess the hazards and risks associated with all operational activities (e.g. routine and non-routine, complex operations) as a precondition to provide safe and healthy workplace. H&S is about conducting a prior risk assessment for any operation.
- Define work-related procedures and practices and up to date them considering the risk assessment, regularly reviewed. Putting in place proven reliable barriers and controls to mitigate risks. H&S is an integral part of all activities, daily.
- Train and coach employees prior to start their work-related activities. Implement and develop awareness and competence to fulfil their tasks safely. H&S culture is an attitude that need to be trained and encouraged.
- Learn from accidents and near misses and share experiences with employees. Investigate and report the root causes rigorously. H&S is to learn from failures as well as successes.
- Comply with all applicable local, regional, national and international Health, Safety and Environment legislation as well as corporate guidelines and rules. Review regularly workplaces and tasks to ensure the compliance. H&S compliance is mandatory and must be constantly guaranteed at all levels of responsibility.
- Monitor, audit and review regularly the adequacy and effectiveness of OH&S management system, procedures and performances according to reference indicators and Group guideline. Define and implement any necessary corrective measures. H&S is to focus on continuous improvement.
- Develop a relationship of constructive cooperation, based on utmost openness and trust, both within the group itself and vis-à-vis the external community and the Institutions in the management of health and safety topics. H&S is to promote transparency and collaboration.
Watch the video dedicated to "One Group"
Safety performance of LWCC
Lehigh White Cement strives on constantly working to improve safety performance and learn from past incidents to ensure a culture of seeing safety as a journey that is never over. There is always room to work to prevent accidents and do better. Performance has improved in terms of lost time injury (LTI) frequency and severity rates through the implementation of Group Guideline on safety and health as well as proactive safety improvements in both the operations of the plant and the culture all workers subscribe to.
Employees | 2023 | 2022 | 2021 | 2020 | 2019 |
---|---|---|---|---|---|
LTI FR (Lost Time Injury Frequency Rate) [injuries with working days of absence/hours worked] x 1,000,000 |
0.0 | 0.0 | 0.0 | 9.5 | 13.4 |
LTI SR (Lost Time Injury Severity Rate) [working days of absence/hours worked] x 1,000 |
0.0 | 0.0 | 0.0 | 0.36 | 0.83 |
Health & Safety Management System
Lehigh White Cement achieved certification for its two manufacturing sites with the ISO 45001 standard for Health and Safety Management Systems. LWCC utilizes an ISO-compliant management system to continually improve on its safety programs, track safety performance, identify hazards & risks, and assess areas to build on strong foundations in its safety culture. LWCC plans to certify its other industrial sites by the end of 2024 completing the certification program.